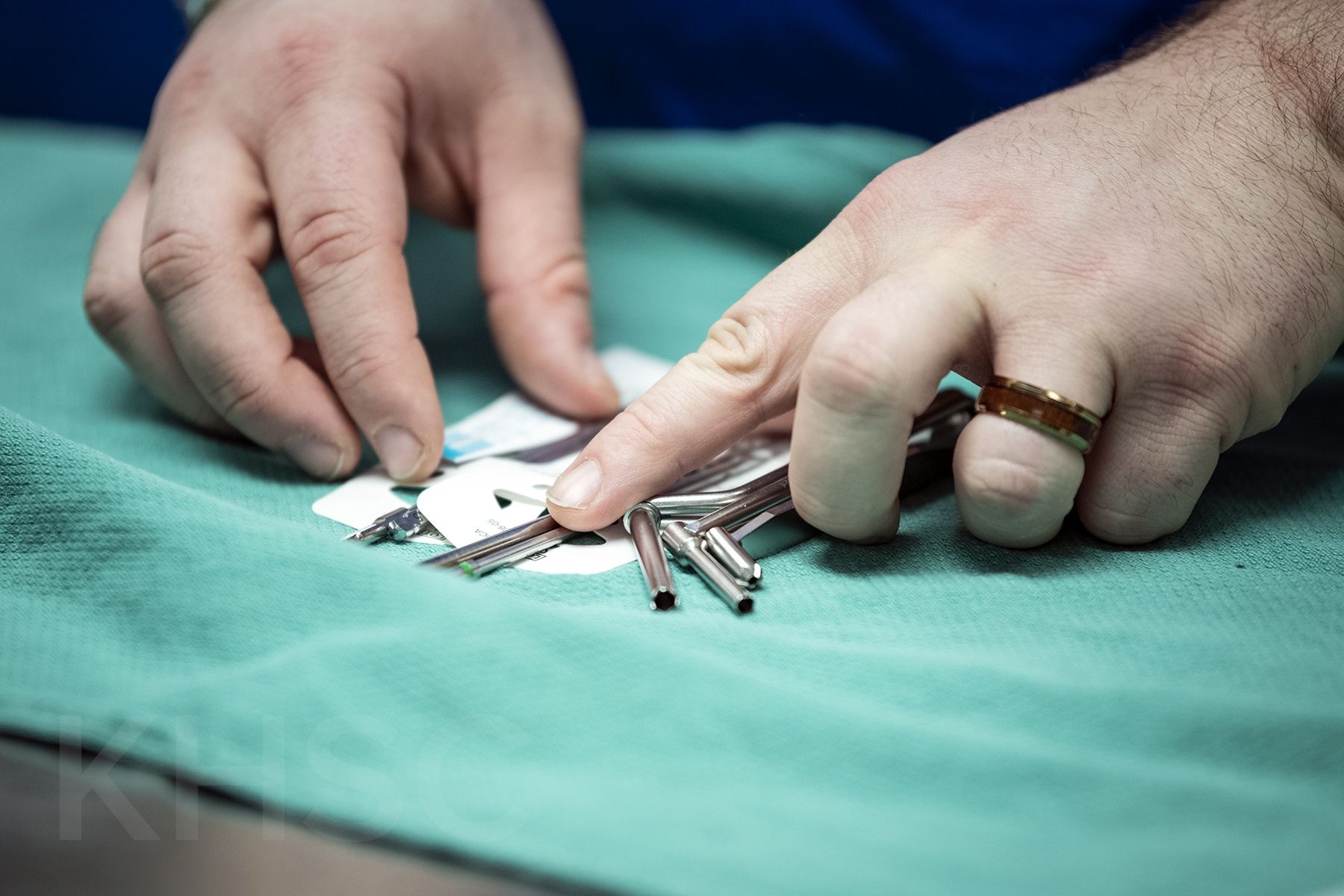
It takes good hands to steer Kingston Health Sciences Centre through an emergency such as the recent flooding in the Central Processing Service (CPS), which sterilizes the instruments used for surgical procedures. Fortunately, those hands are plentiful and steady, with dozens of managers and front-line staff now meeting daily to tackle the task of keeping CPS and our Operating Rooms (ORs) up and running.
The work of that incident management team ripples outwards, with front-line staff in more than 15 areas and departments across the organization stepping up to return us to full surgical capacity. Here’s a snapshot at what staff are saying—and accomplishing—in a few of those affected areas:
CENTRAL PROCESSING SERVICE
CPS has a designated “war room,” a conference room close to the ORs whose walls are covered with need-to-know information—schedules, updates, duties and more, plus space to jot down ideas and suggestions. At a recent huddle—for now, there are three each day—it was clear that CPS staff are up for the challenge facing them every day. Here’s what staff are saying:
- “Being on the forefront of an event like this has been a really valuable experience. We’re seeing how work is delegated, how our skills can be used in different ways and what it means to be part of a big, collaborative team effort.”
- “The HDH site has been great about accommodating us as they run 24/7.We now have a better sense of what they do and they have a better understanding of our volumes and instrumentation.”
- “It been nice having a change of environment by working at the HDH site.They do things a bit differently so we have to adapt a bit but that’s a good challenge for us.”
- “We’re focused on transportation now—suddenly having to load and off-load trucks, keep manifests and coordinate deliveries.This is a first for us and it’s been a new challenge.”
- “We’ve created the temporary new role of Transport Captain—one person who manages all transportation logistics so that the right carts get on the right transport at the right time and land at the right location.One person started in this role but then he taught others on the CPS team so now everyone can do it.It’s working beautifully—no glitches.”
- “It feels like this is bringing us closer to the OR nurses.We normally deal with them on a regular basis but now we’re literally in their space because CPS equipment is being stored in the ORs.They’ve been excellent at working with us and coordinating equipment needs.”
- “It has been stressful but I feel more appreciated and recognized for the work we do in CPS.There’s a stronger sense of being part of a team with the OR.”
“I’m so proud of this team,” says Maria Martins, CPS Supervisor at the KGH site. “They’ve been incredible. No word in the dictionary to express my gratitude. They have been real troopers.”
“Everyone has stepped up,” says Bev McLean, CPS Program Manager. “All the overtime and movement between sites has been voluntary.
“You know, it takes 17 days to break a habit and 27 days to form a new one. This CPS team had just 17 hours from the time we decanted our space to when we ramped back up to 75 per cent of OR activity during the March Break week. Just phenomenal.”
PERIOPERATIVE
Janice Hogeboom, an OR Equipment Technician, makes no bones about the enormity of the task that faced KHSC at the outset.
“We had to move and temporarily store the equivalent of half a football field of instrumentation, disposables and staff belongings from CPS into three ORs and the Burr Gym,” she says. “And everything shifted around as we made room so at times we felt a bit disorganized.
“At the same time, we’ve felt well supported by management, nurses and surgeons. Everyone has been incredibly understanding and accommodating.”
“At first, we were definitely on pins and needles every day to make sure we had coordinated available equipment with the priority cases,” says Charge Nurse Melissa Copas.
“But as we communicated more and more with the physicians and put additional processes in place, you could feel the team really coming together.”
FACILITIES & MAINTENANCE
Since the Code Brown incident, staff and contractors have been working flat out to get the CPS area up and running again, says Gary Greene, Facilities Manager at the KGH site.
“The affected sheet vinyl flooring has been stripped from the floor and the concrete surface prepped for an epoxy product that is much more resilient,” he says, “and extensive infection control barriers are being put in place around the areas under construction. We’ve also replaced 560 ceiling tiles.”
But a bigger task—literally—was prepping for the arrival of a 52-foot mobile sterilization unit on March 19, which is now parked adjacent to the loading docks on King Street.
“That came with many challenges in regards to providing power to it at 480 volts and 300 amps, hot and cold water supplies, sprinkler systems and sufficient drain capacity,” says Greene. “Plus we had to construct an enclosed ramp and decking for the unit so that we could wheel instruments in and out of it from the loading dock area.
For staff, the gleaming mobile unit fits like a glove.
“The washers, sterilizers and processes are the same as those we use in house,” says Martins. “Our staff are pros and know what they’re doing. They just want to be there for the patients and this mobile unit is making that happen.”
“This has been an around-the-clock job for Maintenance staff who are committed to getting CPS systems back online,” says Greene.
MATERIAL MANAGEMENT
Material Management handles the chain of supplies and inventory as well as purchasing at KHSC. The portfolio is managed through our partnership with Shared Support Services Southeastern Ontario (3S0).
As Supply Chain Manager, Ann Van Herpt landed in the middle of supporting the logistical and planning side of recovery efforts, everything from organizing transport of instrumentation between hospital sites to contracting off-site reprocessing services to sourcing disposable instruments.
“Our job has been to leverage existing contracts with vendors wherever possible, which involved working closely with Risk Management to review all contractual obligations,” she explains. “And the team has worked to ease the load by arranging to clear and store some of the bigger pieces of CPS furniture that had ended up in hallways along with coordinating food services for staff working overnight at the HDH site.”
“I’m proud of how the 3S0 team has really stepped up. We see ourselves as an extension of KHSC and feel the pain our sites are going through. For us, it has been all hands on deck and being as supportive as possible at a stressful time.”
KHSC expects to be running 10 ORs at the KGH site this week and anticipates re-opening the CPS on April 13.
Gallery
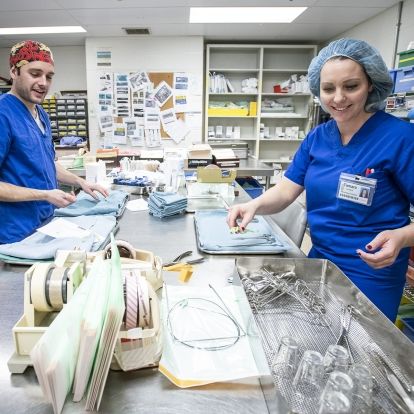
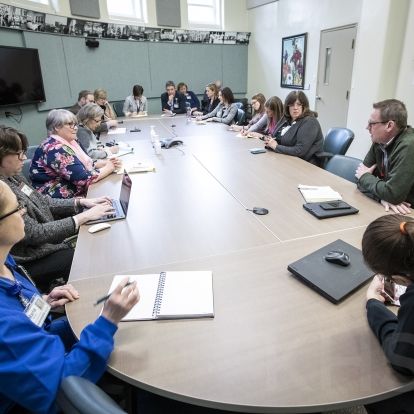
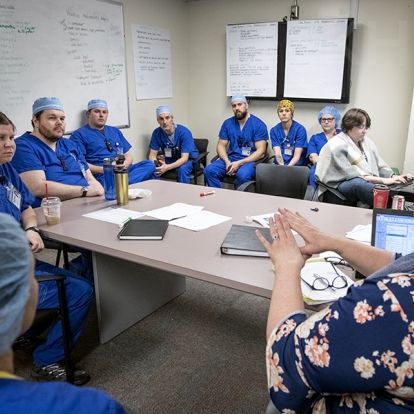
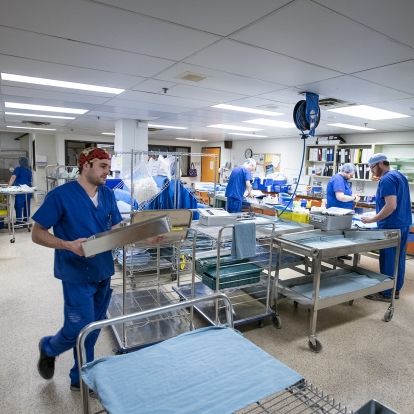
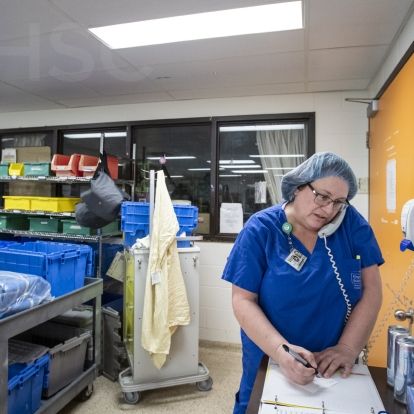
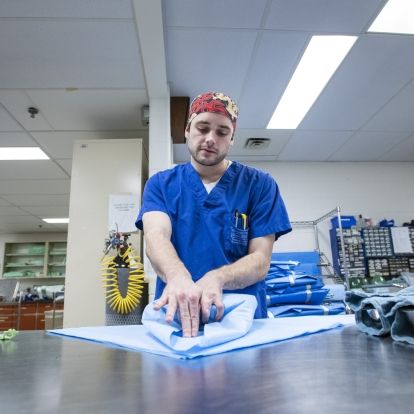
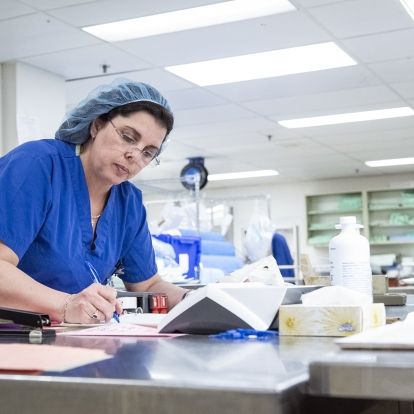
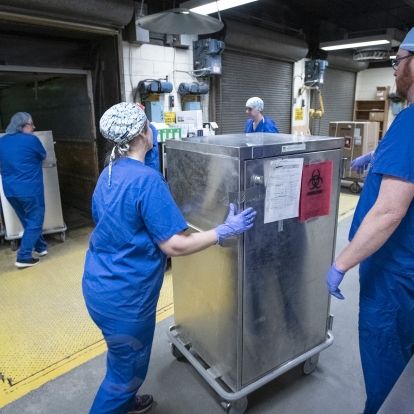
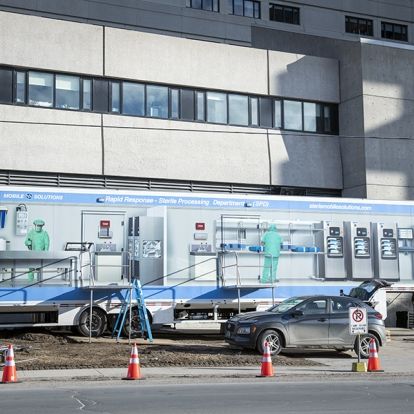
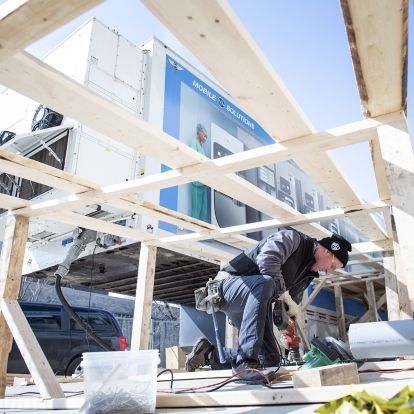
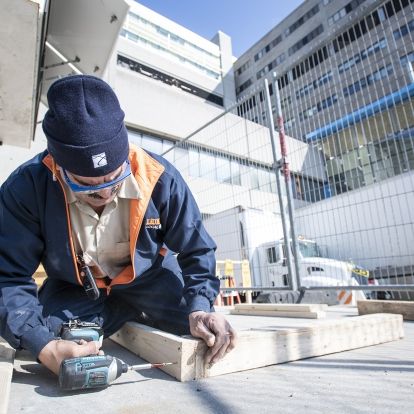
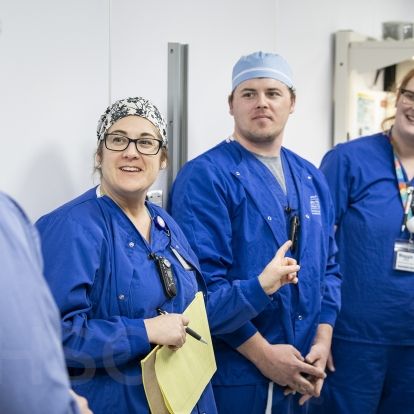
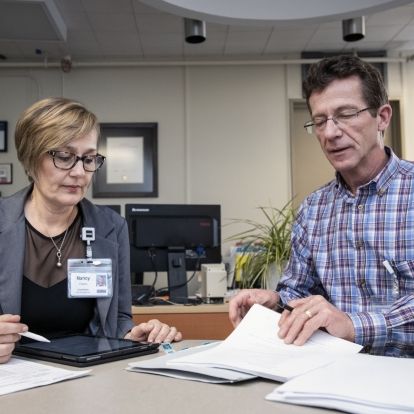
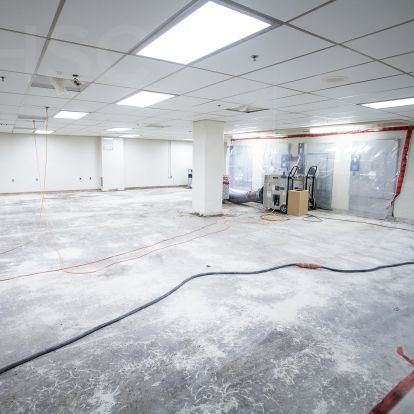
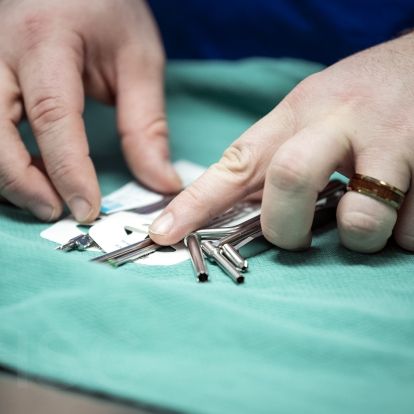
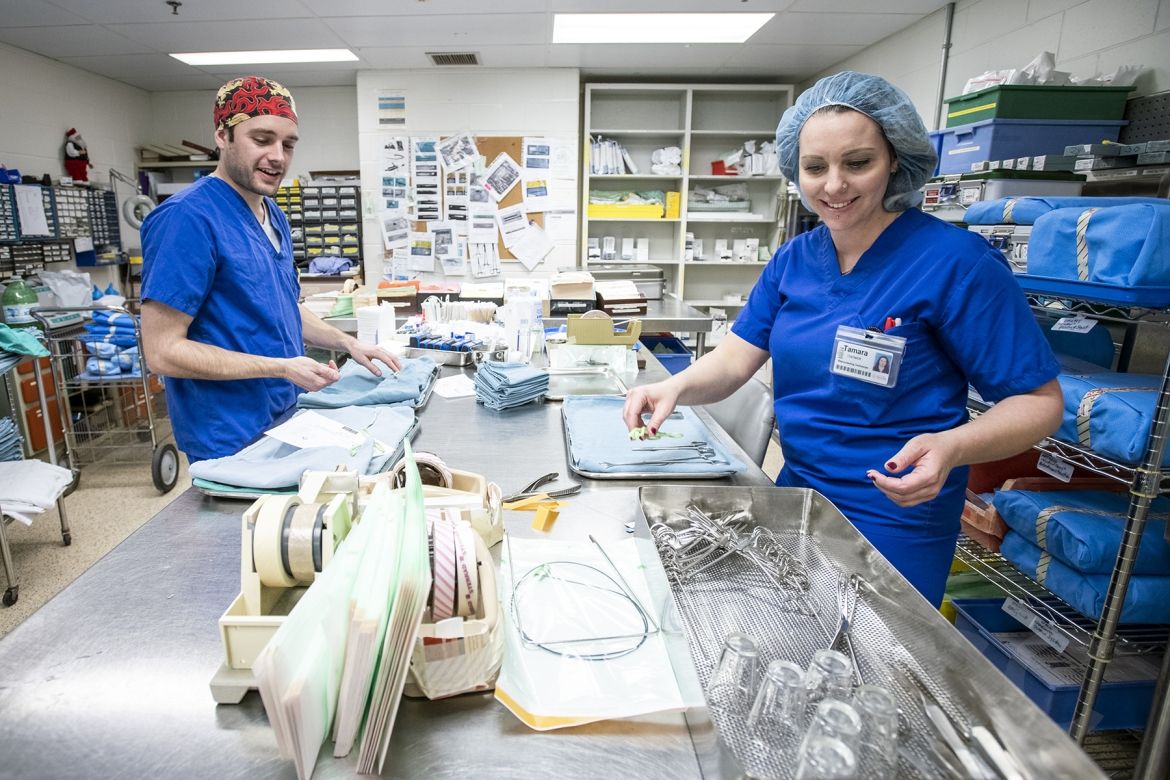
Our HDH site ramped up to 24/7 service to help reprocess surgical instruments. Technicians Jon Reid and Tamara Hartwick work on instrument trays that ultimately will be returned to the KGH site.
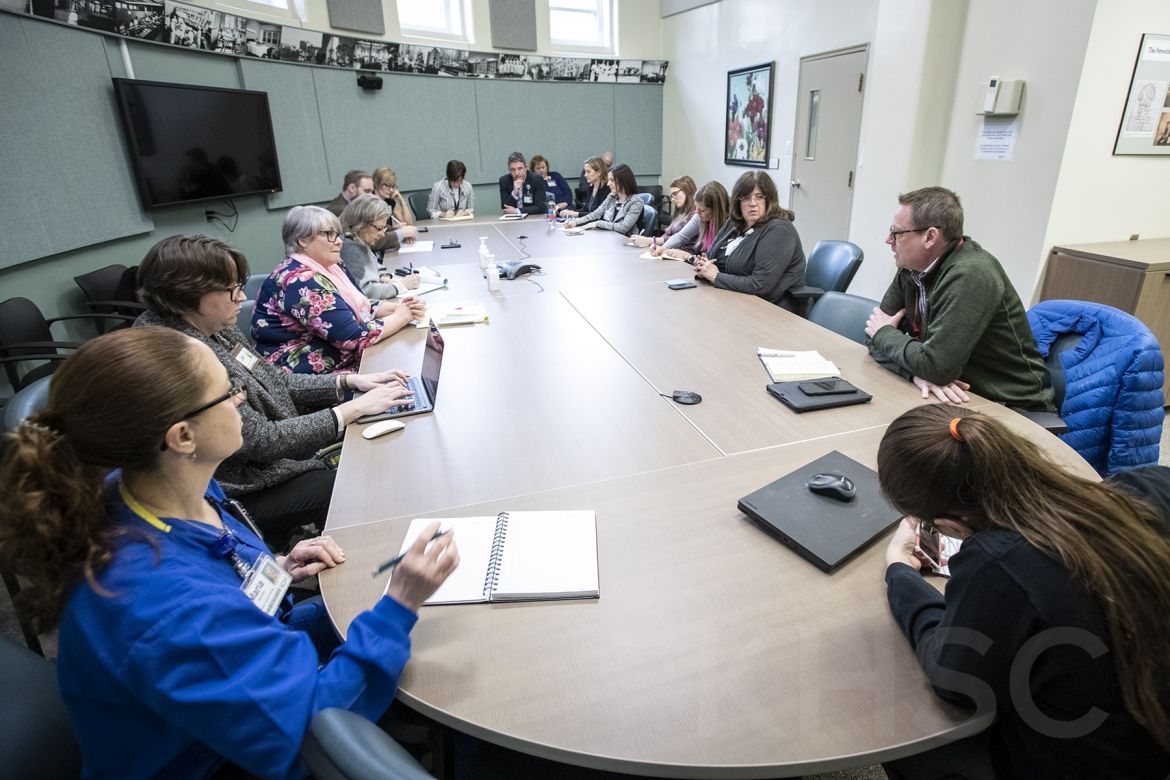
Every day, an Incident Management team gathers to monitor progress of bringing the Central Processing Service back up to full speed at KGH.
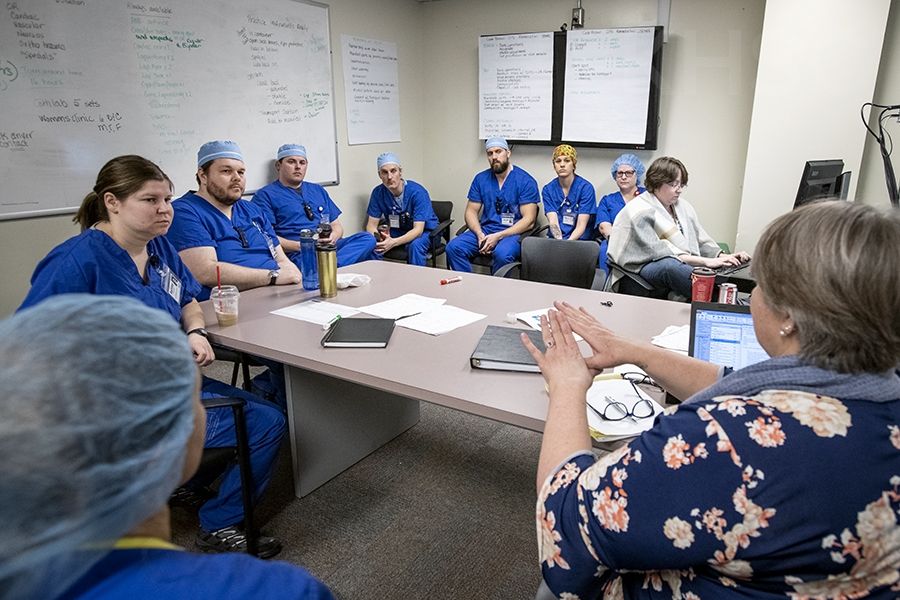
Three times daily, staff from the Central Processing Service at KGH huddle for the latest updates, scheduling and planning geared to keep sterilized instrumentation and equipment flowing to the Operating Rooms at KGH.
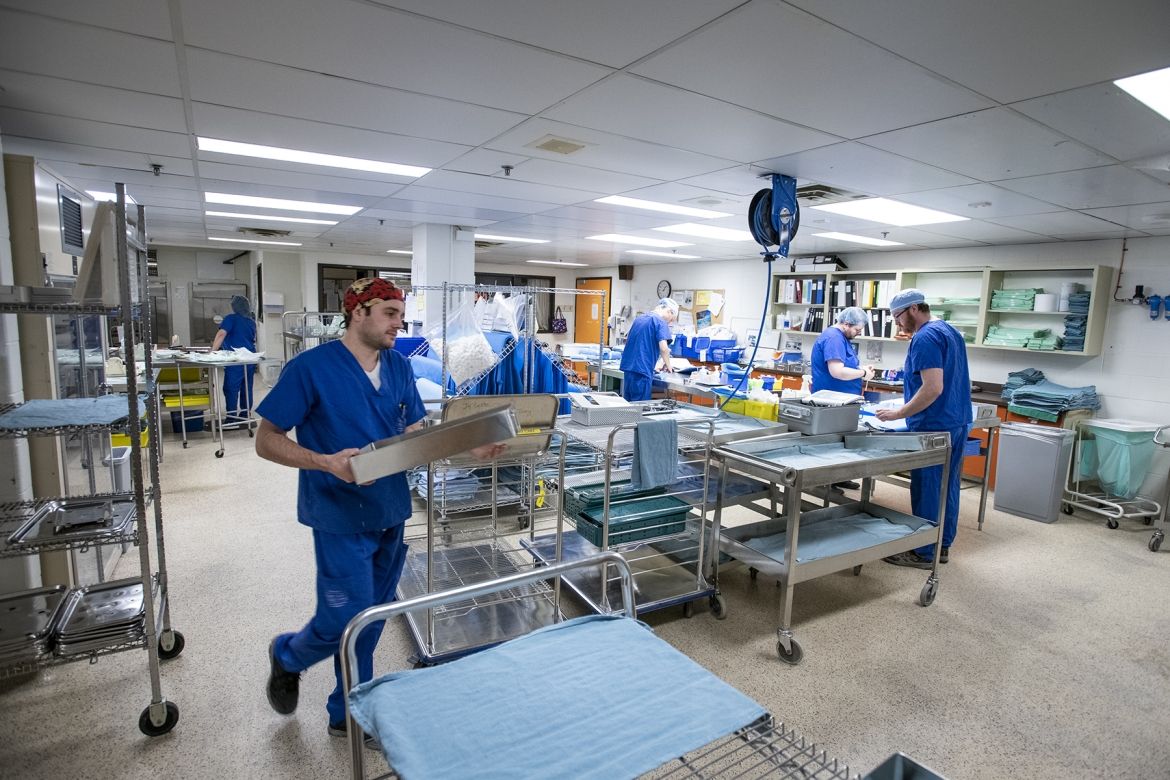
Central Sterilization Reprocessing at the HDH site has been running 24/7 to keep instruments flowing to the ORs at KGH.
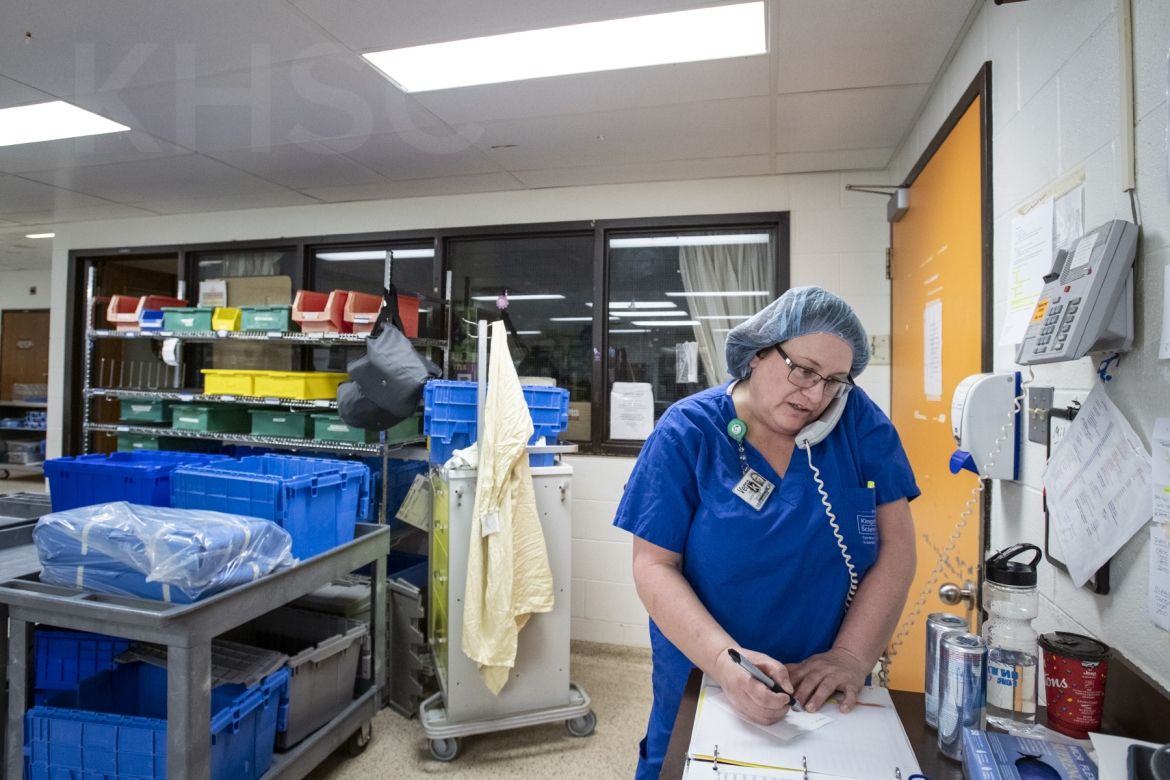
Central Processing Service assistant/technician Verna Harper tracks instrumentation traffic between the two KHSC hospital sites.
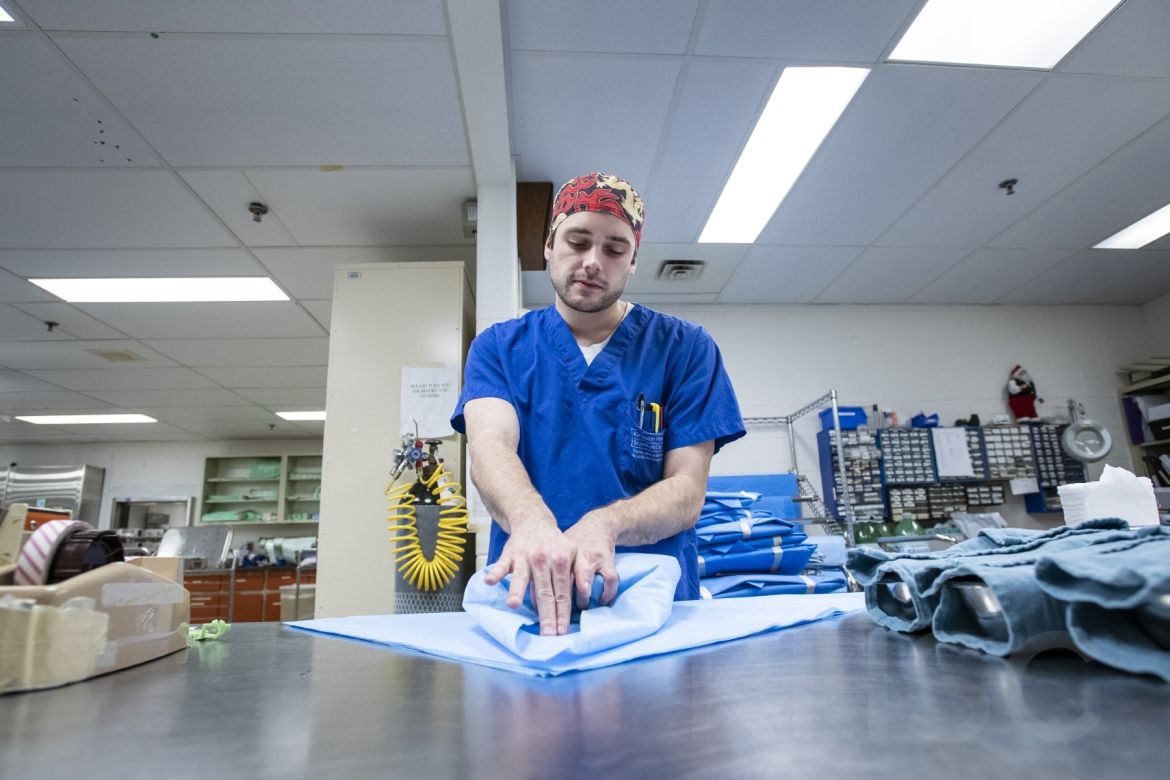
At the HDH site, Central Sterilization Reprocessing technician Jon Reid carefully wraps a tray of sterile instruments.
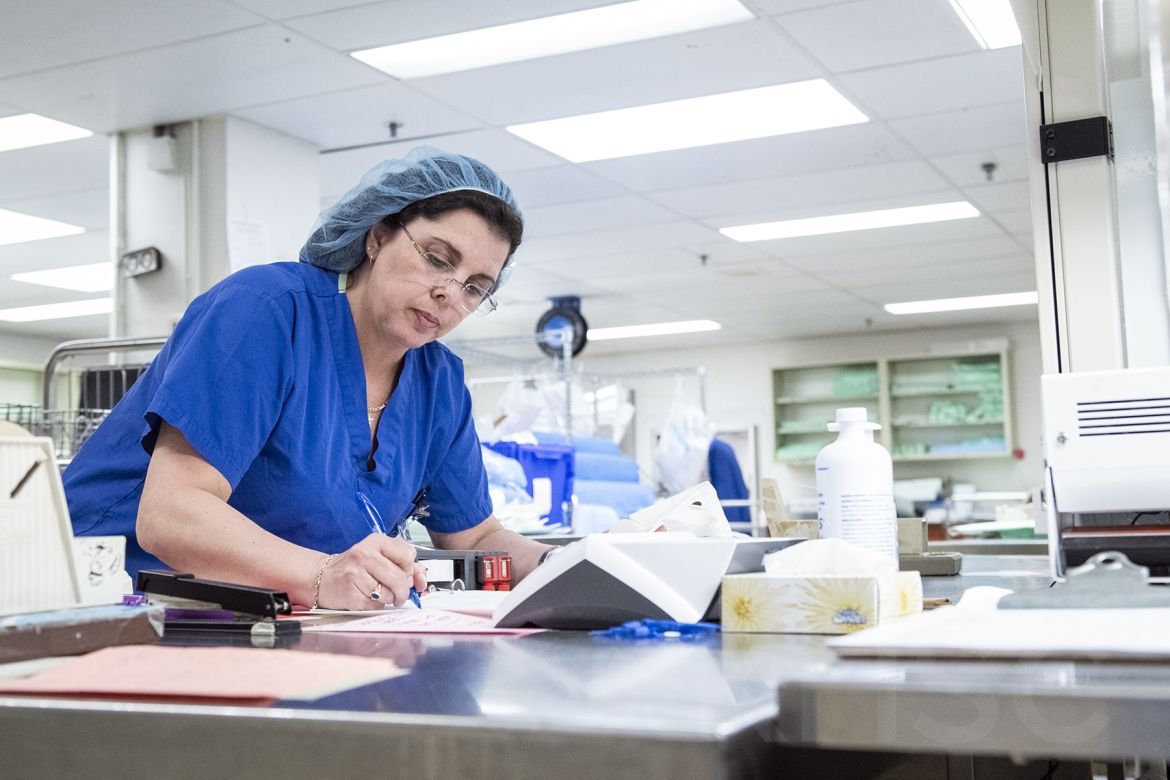
At the HDH site instrument technician Anna Neves checks the day’s instrumentation manifest.
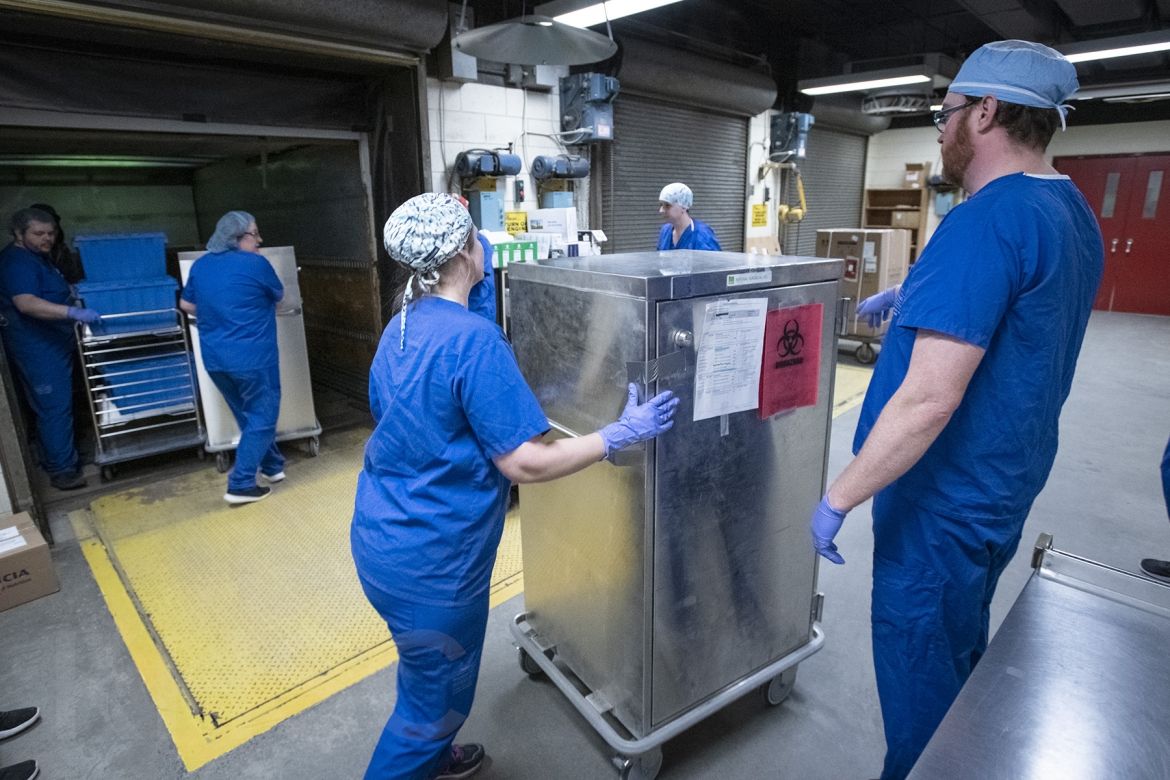
It’s all hands on deck as instrument technicians at the HDH send the latest load of sterilized equipment out the door and on its way back to the KGH site for surgical services.
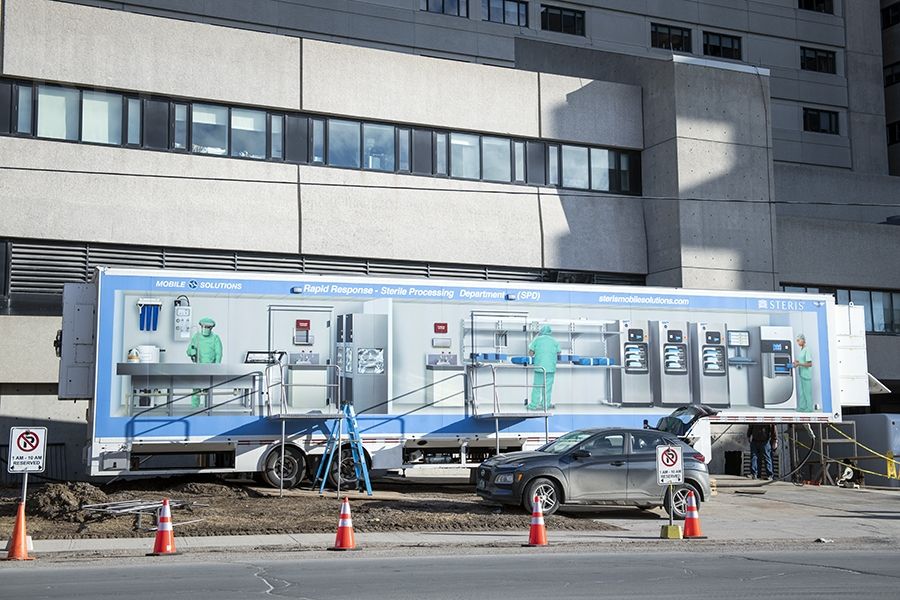
The 52-foot-long Steris mobile sterilization unit arrived March 19 and was hard to miss parked on the south side of the KGH site.
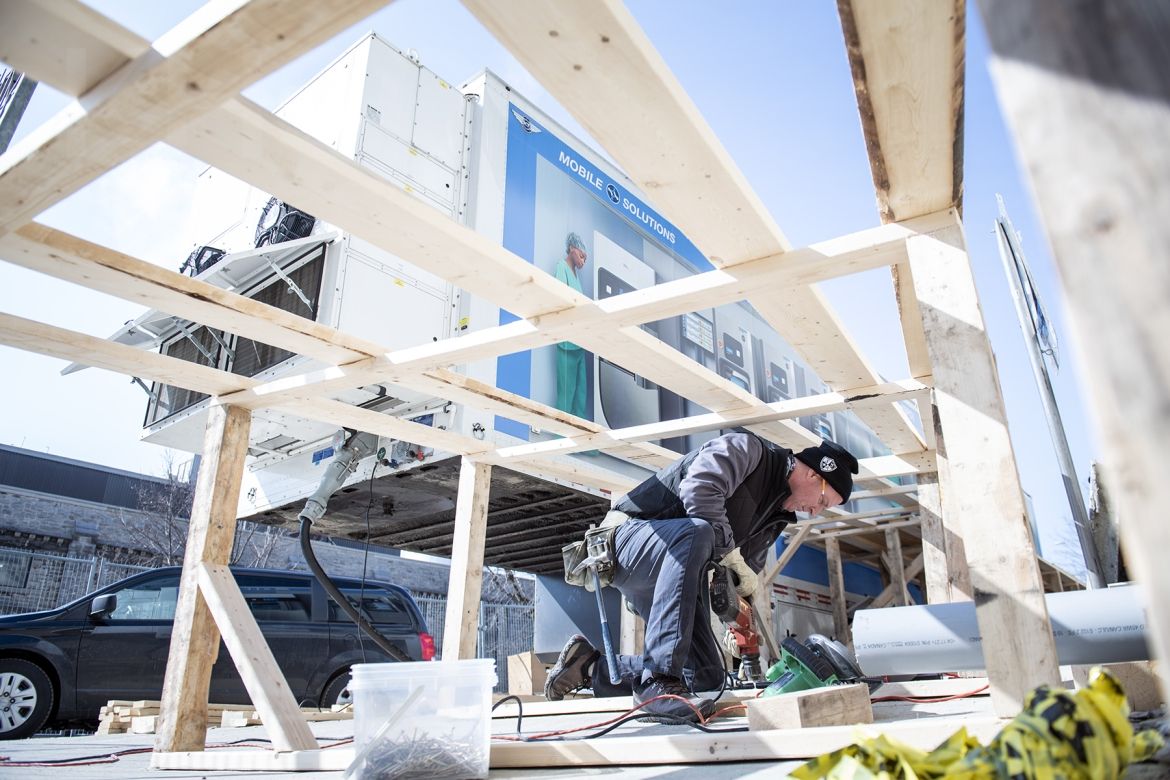
With the mobile sterilization unit looming behind him, KHSC carpenter Mike Berry works on constructing a covered ramp between the unit and hospital.
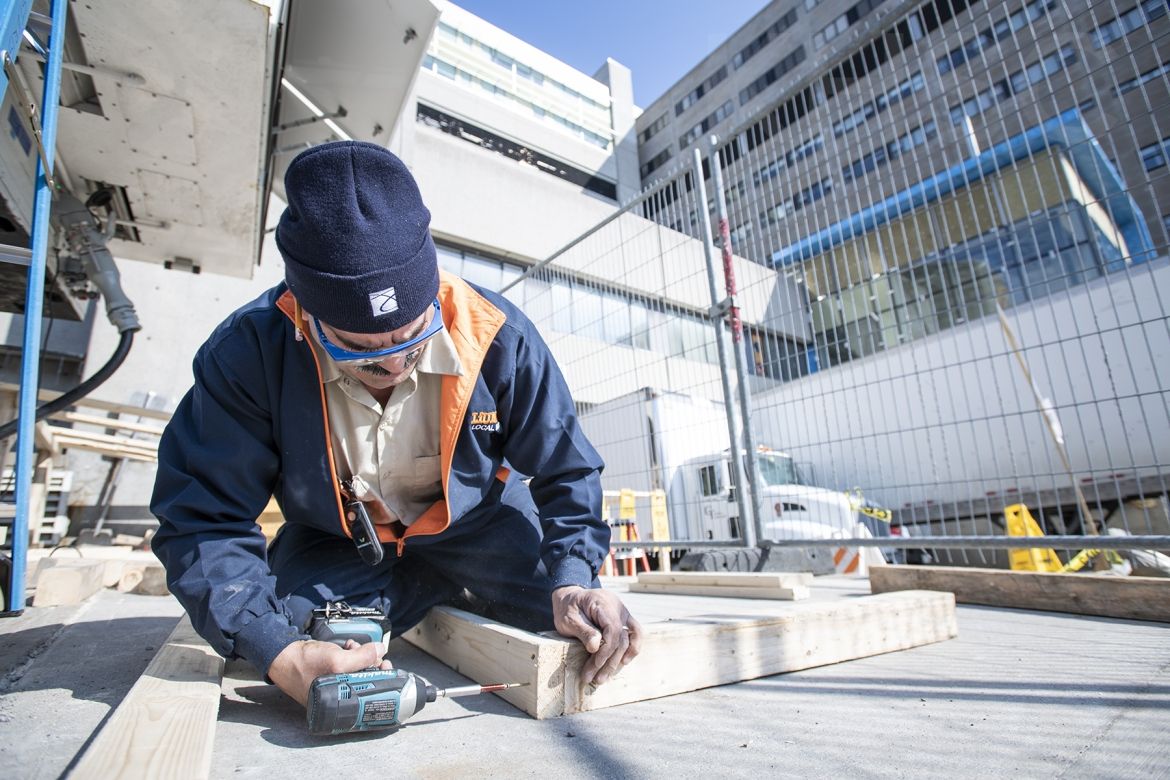
KHSC carpenter Dave DeSousa was part of a building crew that mobilized quickly to build a walkway between the Steris mobile unit and loading dock at the KGH site.
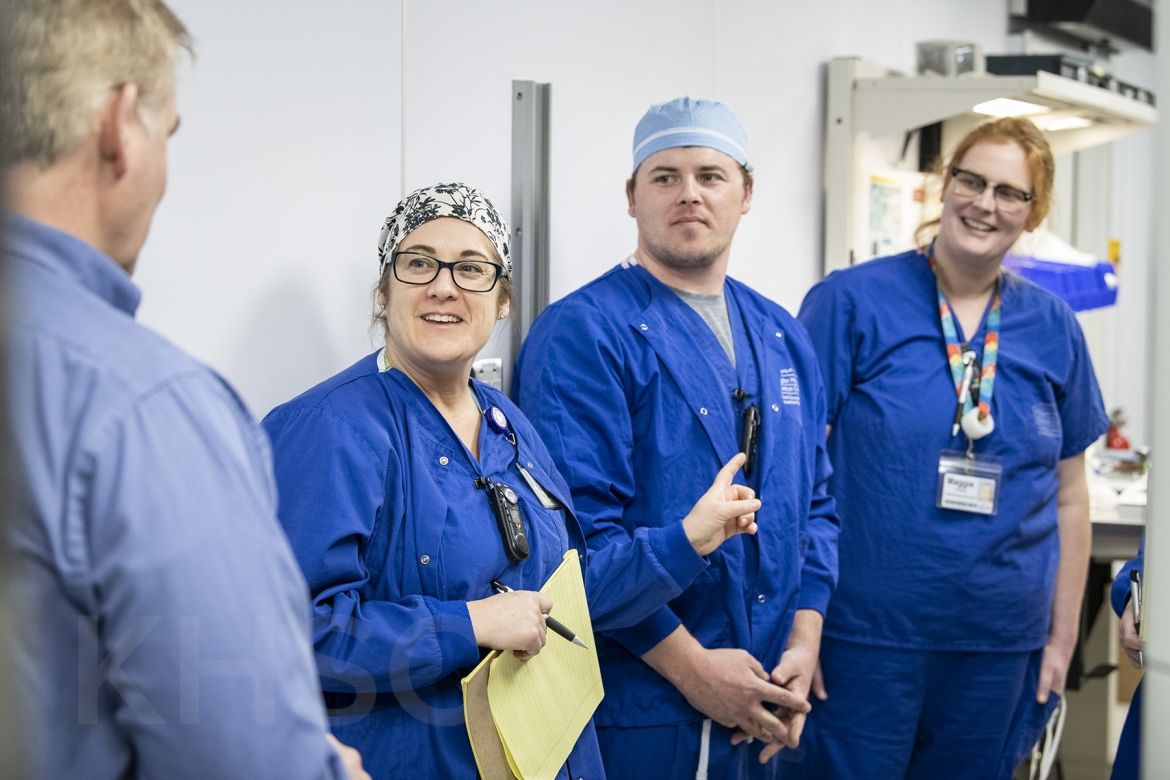
Getting some training on the newly-arrived mobile sterilization unit are reprocessing technicians (l to r) Tara Reynolds, Cody Lloyd and Maggie Hearns.
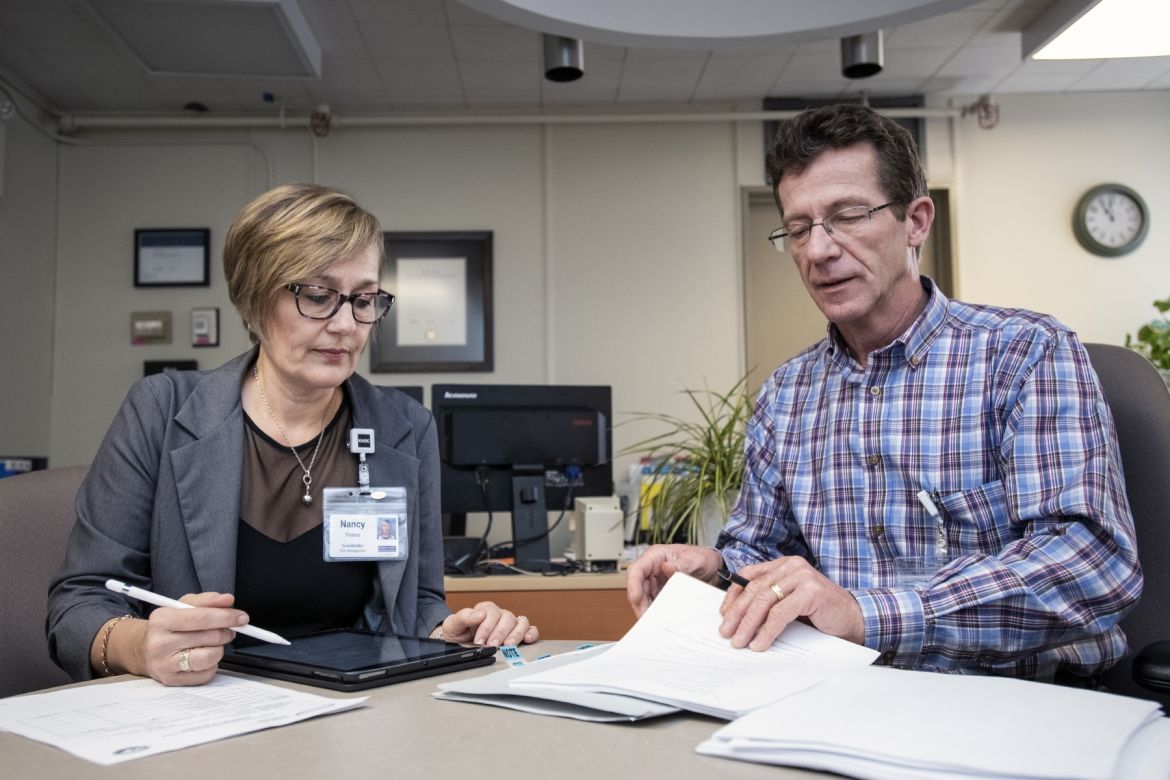
Risk Management staff Nancy Peters and Steve Snable pore over documentation regarding the costs and contracts involved in maintaining sterilization services at KHSC's KGH site.
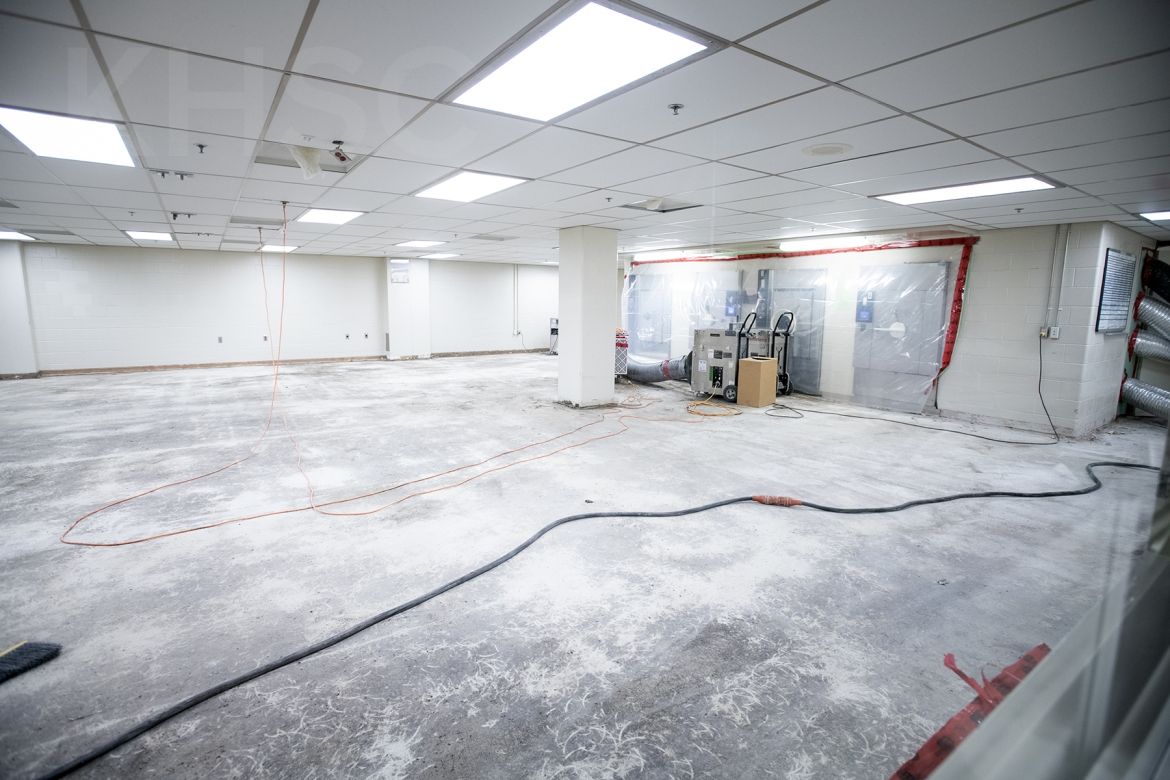
Meanwhile, repair and remediation work is proceeding quickly in the Central Processing Service at KGH, expected to be back in full service April 13.
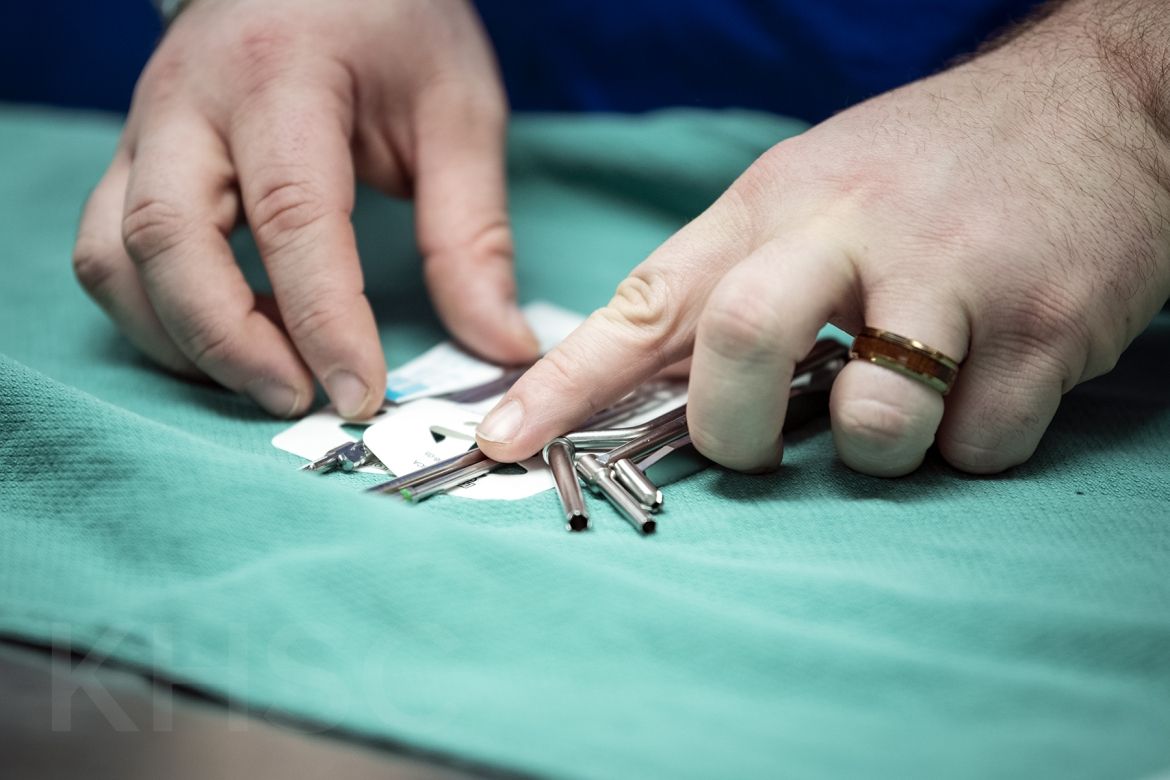