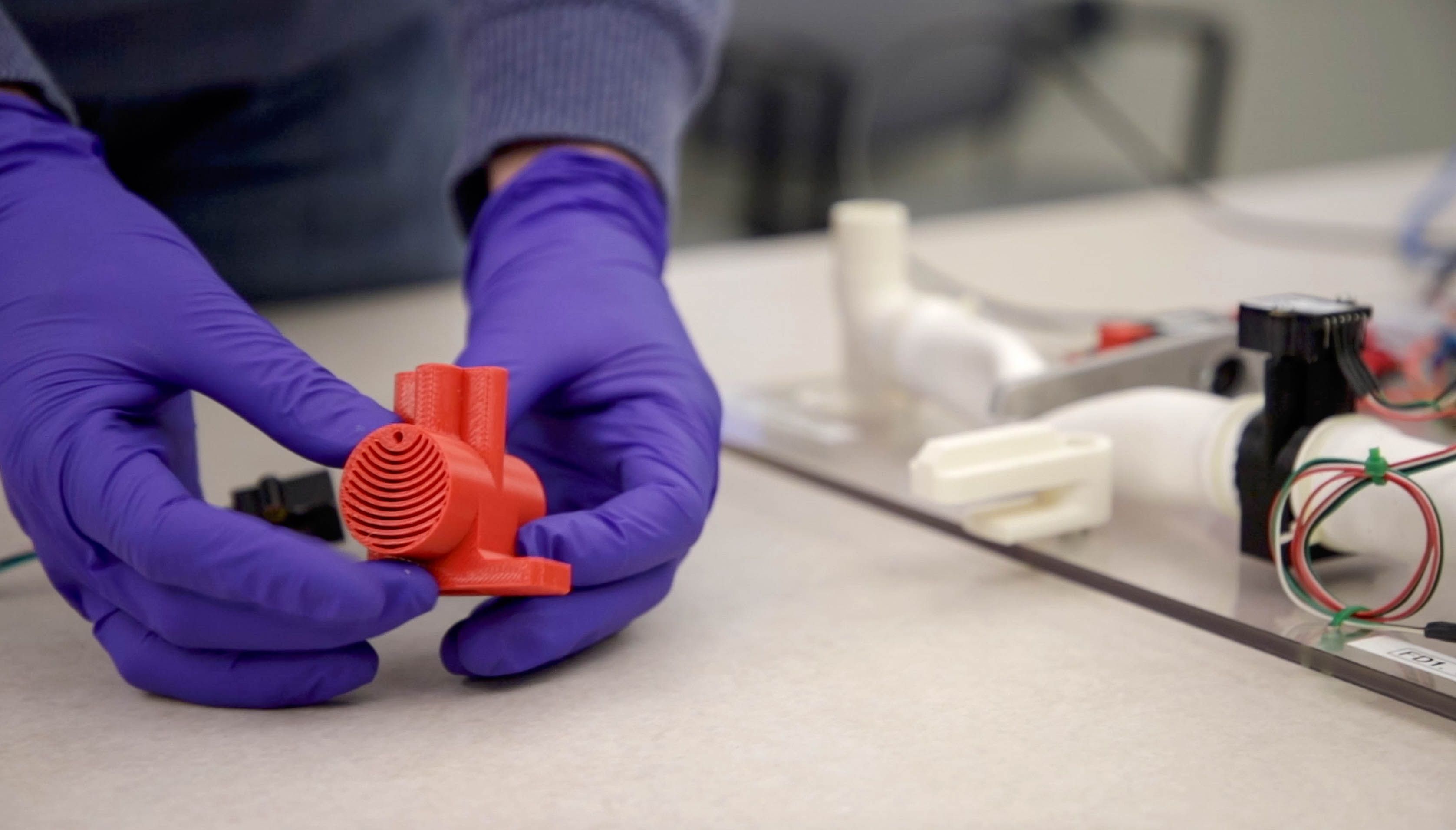
A Queen’s University / Kingston Health Sciences Centre (KHSC) team of students, staff, faculty and health professionals is one of the nine finalists in the prestigious Code Life Ventilator Challenge. The Kingston team competed against over 1,000 teams from 94 countries working non-stop over two weeks to create the “YGK Modulator Ventilator”, a low-cost and easy-to-manufacture ventilator that can be deployed anywhere around the world.
“I’m so proud of the team and their commitment to finding solutions during this crisis,” says Dean Kevin Deluzio of the Faculty of Engineering and Applied Science. “They are an excellent example of how Queen’s and Kingston’s health professionals collaborate and innovate. Multidisciplinary engineering teams like these will be the gamechangers as we take on this pandemic.”
The Code Life Ventilator Challenge was initiated by the Montreal General Hospital Foundation and the Research Institute of the McGill University Health Centre in response to the COVID-19 crisis. The final prototypes are currently being tested by the competition’s judges, and the top three winning designs, which will be announced this week, will be posted online for free download by anyone who wants to use them.
The team’s design features Continuous Positive airway Pressure (CPAP) machines, which are commonly used by people with sleep apnea. Two of the devices were paired together to provide the air pressure required for a ventilator, with the supply of air controlled by a series of tubes and mechanical arms that operate using a small computing device. The materials in the design are easy to source, swap out, or print using a 3-D printer.
The design team includes students, staff and faculty from across several engineering disciplines including Ingenuity Labs, the Human Mobility Research Centre, Mechanical and Materials Engineering, Electrical and Computer Engineering, the RCV Lab, and the Queens Formula SAE team. Health professionals from KHSC and staff from its Ventilator Equipment Pool provided invaluable expertise during the two-week scramble to create a design and then refine it for the second round.
Community members donated dozens of CPAP machines to build the prototypes. Medigas and FPM Solutions also provided machines and technical expertise during the design phase.
“I was so impressed by the dedication of our team members, especially our students,” says team co-lead Tim Bryant, Professor Emeritus, Department of Mechanical and Materials Engineering. “They were spending countless hours on this challenge, all while still in classes, completing assignments, and writing exams. Our health care partners are busy at the hospital, but always made time to provide guidance in the design and testing phases.”
“It was an amazing experience to be part of this,” says Sonja Pejcic, a Master’s candidate in the department of Mechanical and Materials Engineering. “We’ve done many group projects as part of our undergraduate studies, but this was a real-life situation that required intense collaboration and cooperation. It was an honour to be part of this team.”
Learn more about the Code Life Ventilator Challenge
Gallery
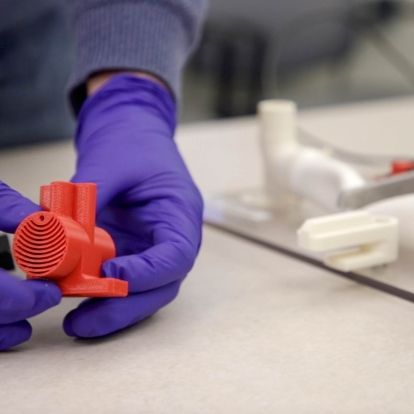
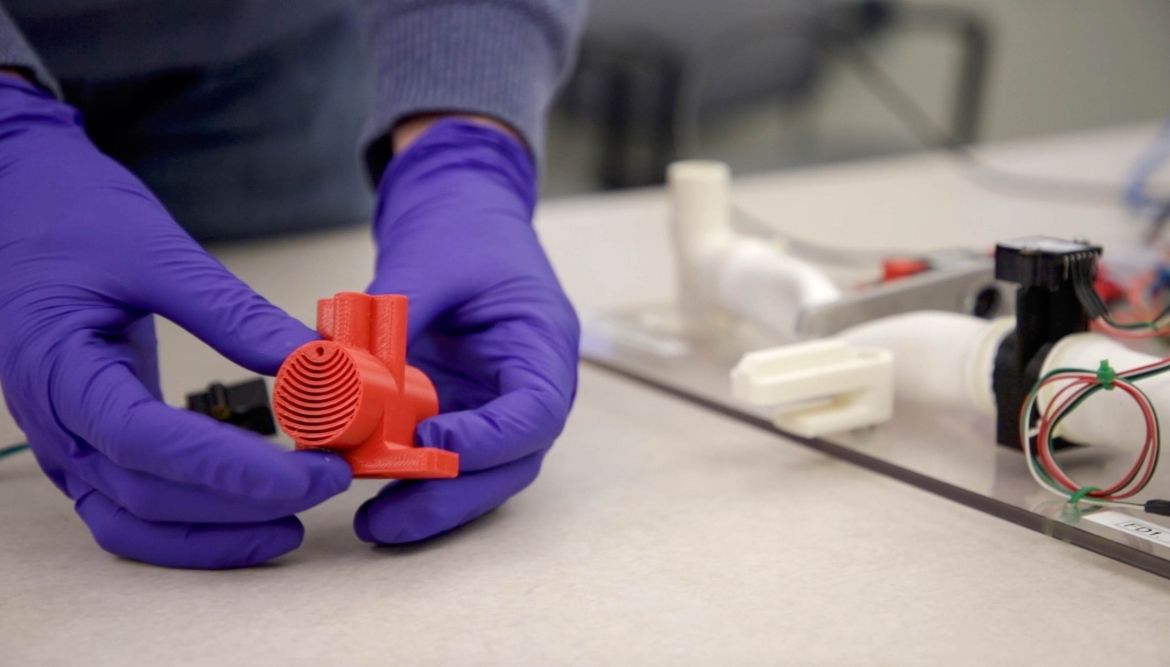
One of the advantages of the YGK Ventilator is that many of its parts can be 3D-printed.